Radon Gas Mitigation Systems Information
How to Remove Radon Gas
Soil gas radon enters structures through openings in the foundation. The radon gas concentration in any building is determined by the radon concentration in the soil, soil permeability, and the pressure differential between the soil and the building.
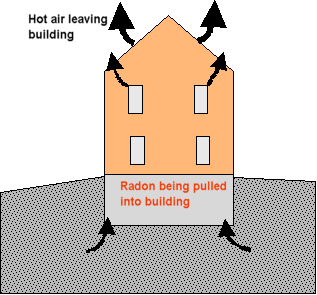
Almost all buildings exert a negative pressure (suction) on the soil because of the natural stack effect and exhaust devices that exist in all buildings. The stack effect is the same phenomenon that occurs in a chimney. Hot air rises and leaves the top of the building. The replacement air is pulled in at the bottom of the building. This pull (suction) brings in the soil gas. Of the three factors (concentration, permeability, and pressure) the only one that can be controlled in an existing building is the pressure. If the pressure under the concrete slab can be made to be less than the building’s pressure, the soil gas will not enter the building.
WHAT IS DONE TO TREAT SOIL GAS RADON?
Sub-slab depressurization systems create negative pressure under the slab that prevents the soil gas from being drawn into the building. To do this, pipes are inserted through the slab and routed to the exterior of the building. A fan is placed on the pipe and the exhaust is then routed to a safe area above the building. The fan pulls air from under the slab. Removing the air creates a negative pressure (suction) under the slab that is greater than the negative pressure (suction) exerted by the building. This negative pressure (suction) prevents the radon from entering the building.
The treatment for dirt floor basements and crawl spaces is similar to that for areas with slabs. In the case of a crawl space, a fire retardant plastic membrane provides the barrier the slab would normally create. Air is then drawn from under the membrane to create the negative pressure that prevents the entry of the gas.
WHY USE A REGISTERED CONTRACTOR?
All radon systems must meet certain minimum requirements to be safe. A registered mitigation contractor must comply with more than 140 regulations to install a system that meets the requirements set by the EPA. The average consumer should know some of the most basic system requirements to ensure they are getting a safe and reliable system.
THE FAN CAN NOT BE BELOW THE LIVING SPACE.
The gas that is pulled from under the slab can have very high concentrations of radon gas (several 1000 pCi/L) and any leak on the exhaust side of the fan can cause very high levels of radon to be released. This is why the fan should never be put in the basement. There are three common locations for the fan – outdoors on the side of the building, in a garage or in the attic of the house.
THE EXHAUST PIPE OUTPUT MUST BE ABOVE THE ROOF.
The exhaust output must be in a location that will not allow radon gas to flow back into the structure or a neighboring structure. The exhaust output must be at least 2 feet above or 10 feet away from any potential re-entry point such as a window or bathroom exhaust vent.
THE SYSTEM MUST HAVE A MONITOR THAT INDICATES THAT THE FAN IS OPERATING.
A manometer, also known as a vacuum monitor, is attached to the exhaust pipe to indicate whether the fan is working to properly pull gases from under the slab or membrane. This simple device is most often installed on the pipe in the basement.
THE GARAGE WALL PENETRATION SHOULD BE FITTED WITH A UL-LISTED FIRE STOP.
The wall between all attached garages and homes is fire rated and its integrity should be maintained by installing a UL-listed fire stop on the pipe where it penetrates the garage wall.
Radon Resources